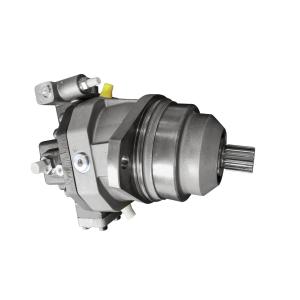
Add to Cart
A6VM28HZ Bent Axis Piston Motor Two-Point Control for Mobile Machinery
Features:
1. High-precision control for industrial equipment
2. Gearless transmission structure
3. Compatibility with eco-friendly hydraulic oils
4. Extreme temperature resistance (-40°C~+115°C)
5. Radial load-bearing capacity of drive shaft
6. Bent-axis design with axial tapered piston rotary group
7. Compatibility with hydrostatic drives in open/closed circuits
8. Dual applicability in mobile and stationary machinery
9. Infinitely variable speed control with wide range
10. Stepless adjustment for displacement from Vgmax to zero
Technical data:
Size | NG | 80 | 107 | 140 | 160 | 200 | 250 | ||
Geometric displacement, per revolution | Vg max | cm3 | 80 | 107 | 140 | 160 | 200 | 250 | |
Vg min | cm3 | 0 | 0 | 0 | 0 | 0 | 0 | ||
Vg x | cm3 | 51 | 68 | 88 | 61 | 76 | 205 | ||
Maximum rotational speed(while adhering to the maximum permissible inlet flow) | at Vg max | nnom | rpm | 3900 | 3550 | 3250 | 3100 | 2900 | 2700 |
at Vg < Vg x | nmax | rpm | 6150 | 5600 | 5150 | 4900 | 4600 | 3300 | |
where Vg 0 | nmax | rpm | 7350 | 6300 | 5750 | 5500 | 5100 | 3300 | |
Inlet flow | at nnom and Vg max | qv max | l/min | 312 | 380 | 455 | 496 | 580 | 675 |
Torque | at Vg max and Δp = 400 bar | T | Nm | 509 | 681 | 891 | 1019 | 1273 | ‒ |
at Vg max and Δp = 350 bar | T | Nm | 446 | 596 | 778 | 891 | 1114 | 1391 | |
Rotary stiffness | Vg max to Vg/2 | cmin | kNm/rad | 16 | 21 | 34 | 35 | 44 | 60 |
Vg/2 to 0 (interpolated) | cmin | kNm/rad | 48 | 65 | 93 | 105 | 130 | 181 | |
Moment of inertia for rotary group | JTW | kgm2 | 0,008 | 0.0127 | 0.0207 | 0.0253 | 0.0353 | 0,061 | |
Maximum angular acceleration | α | rad/s² | 24000 | 19000 | 11000 | 11000 | 11000 | 10000 | |
Case volume | V | l | 1.2 | 1.5 | 1.8 | 2.4 | 2.7 | 3 | |
Weight approx. | m | kg | 36 | 46 | 61 | 62 | 78 | 100 |
Specifications:
Warranty | 1 Year |
Specification | SY-A6VE |
Place of Origin | China |
Type | Agricultural axial piston motor |
Color | Available any color |
HS Code | 8412299090 |
Application | Agricultural machinery (harvesters, tractors) |
Maximum pressure | 450 bar |
Delivery Time | 15-30 Days after Payment |
Displacement | 71-250 cm3 |
Applications:
Competitive Advantage:
1. High Radial Load Capacity: Reinforced bearing housings withstand 15 kN radial forces for conveyor tensioners or gantry cutting machines with heavy side loads.
2. By optimizing internal fluid circuit design and employing precision manufacturing techniques, the Rexroth A6VM hydraulic motor effectively minimizes energy losses and frictional resistance within the hydraulic system, ensuring efficient power transmission and stable output under high-load and high-speed conditions; this axial piston motor delivers a highly reliable, energy-efficient, and cost-effective hydraulic drive solution for automated production lines, CNC machine tools, and logistics systems, greatly enhancing overall system competitiveness.
3. Equipped with flexible control strategies and high-precision sensors, the Rexroth A6VM piston motor achieves real-time monitoring and adjustment of hydraulic parameters, ensuring rapid response to system demands under all operating conditions while minimizing errors and delays; this hydraulic motor optimizes overall system efficiency and provides exceptional performance and operational stability for industrial robotics, automation equipment, and high-end manufacturing sectors.
The Analysis For Rexroth A6VE Piston Motor Common Breakdown:
1.Failure of vibration sensors in the Rexroth A6VE hydraulic motor may prevent timely detection of abnormal vibrations, delaying fault warnings and impacting system stability. Such sensor failures are often related to poor electrical connections or internal component defects. Regular calibration and testing of vibration sensors, along with ensuring proper connections, are vital to improving the accuracy of fault detection in this piston motor.
2. Interference with control signals in the Rexroth A6VE axial piston motor can be caused by strong surrounding electromagnetic fields, poor grounding, or improper wiring layout, leading to data errors or signal loss in the control system. Such interference results in delayed responses or operational mistakes. Implementing shielding, optimizing wiring configurations, and improving grounding conditions are effective methods to reduce signal interference in this hydraulic motor.
3. Sticking Control Piston: High movement resistance may stem from tight clearance (<10 μm) or oil sludge. Lap piston guides and switch to oxidation-resistant fluid.